Saponification à froid vs saponification à chaud
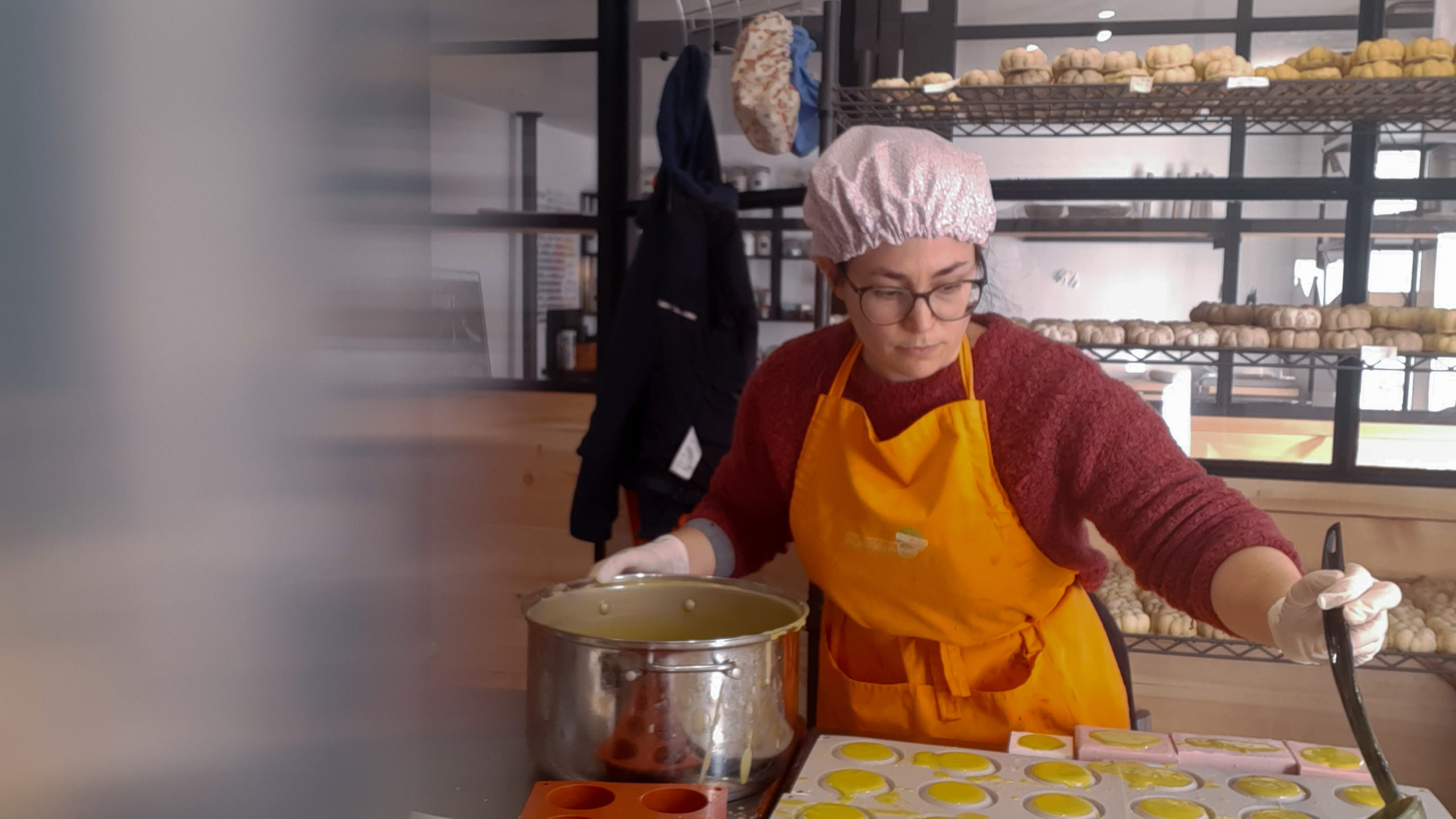
Démarrons avec la saponification à chaud
La saponification à chaud (ou cuisson au chaudron) est un procédé traditionnel de fabrication de savon qui consiste à accélérer la réaction chimique entre un corps gras (huile ou beurre) et une base (soude caustique ou potasse). La méthode implique une chauffe plus élevée que la saponification à froid des matières. Ce processus permet de produire du savon plus rapidement que la méthode de saponification à froid. Il présente quelques avantages uniques.
Étapes du processus de saponification à chaud
Tout comme en saponification à froid, il est nécessaire de préparer les huiles et les beurres qui détermineront les propriétés du savon. Huile d’olive, huile de coco, beurre de karité, etc. déterminent la dureté, le type de mousse et la douceur du savon fini.
En parallèle, préparer la base alcaline, à savoir la soude caustique (hydroxyde de sodium), généralement utilisée pour les savons solides. Pour les savons liquides, la potasse (hydroxyde de potassium) est préférable.
On mélange corps gras et base alcaline dans un récipient. A ce stade, la réaction de saponification commence, mais sera accélérée si l’on chauffe le tout, souvent au bain-marie ou dans un chaudron. La température peut varier, mais elle se situe généralement entre 70°C et 100°C. La chaleur accélère la réaction de saponification, tet transforme les graisses en savon et en glycérine. Ce processus peut durer d’1 à 3 heures.
Cuisson et traçage
Au fur et à mesure que le mélange chauffe, il s’épaissit et passe par plusieurs phases : pâteuse, liquide, puis épaisse et gélatineuse. On atteint la trace (similaire à la saponification à froid) lorsque le mélange devient suffisamment épais. Une trace visible se dessine à la surface lorsqu’on y dessine un motif avec la spatule (similaire à un caramel épais).
Ajout des additifs
La saponification est presque terminée, on peut ajouter des ingrédients comme des huiles essentielles, des fragrances, des colorants, des herbes, des épices, des exfoliants. On effectue ces ajouts à ce stade car la réaction chimique est presque complète. Cela permet de préserver les propriétés des additifs.
Mise en moule et séchage
On verse ensuite le savon dans des moules. Comme la réaction de saponification est déjà avancée, le savon durcit rapidement. Après quelques heures à une journée de repos, on démoule et découpe le savon.
La cure (facultatif)
Bien que la saponification soit essentiellement terminée lors du démoulage, certains fabricants laissent le savon sécher et durcir pendant une à deux semaines pour améliorer sa texture et prolonger sa durée de vie.
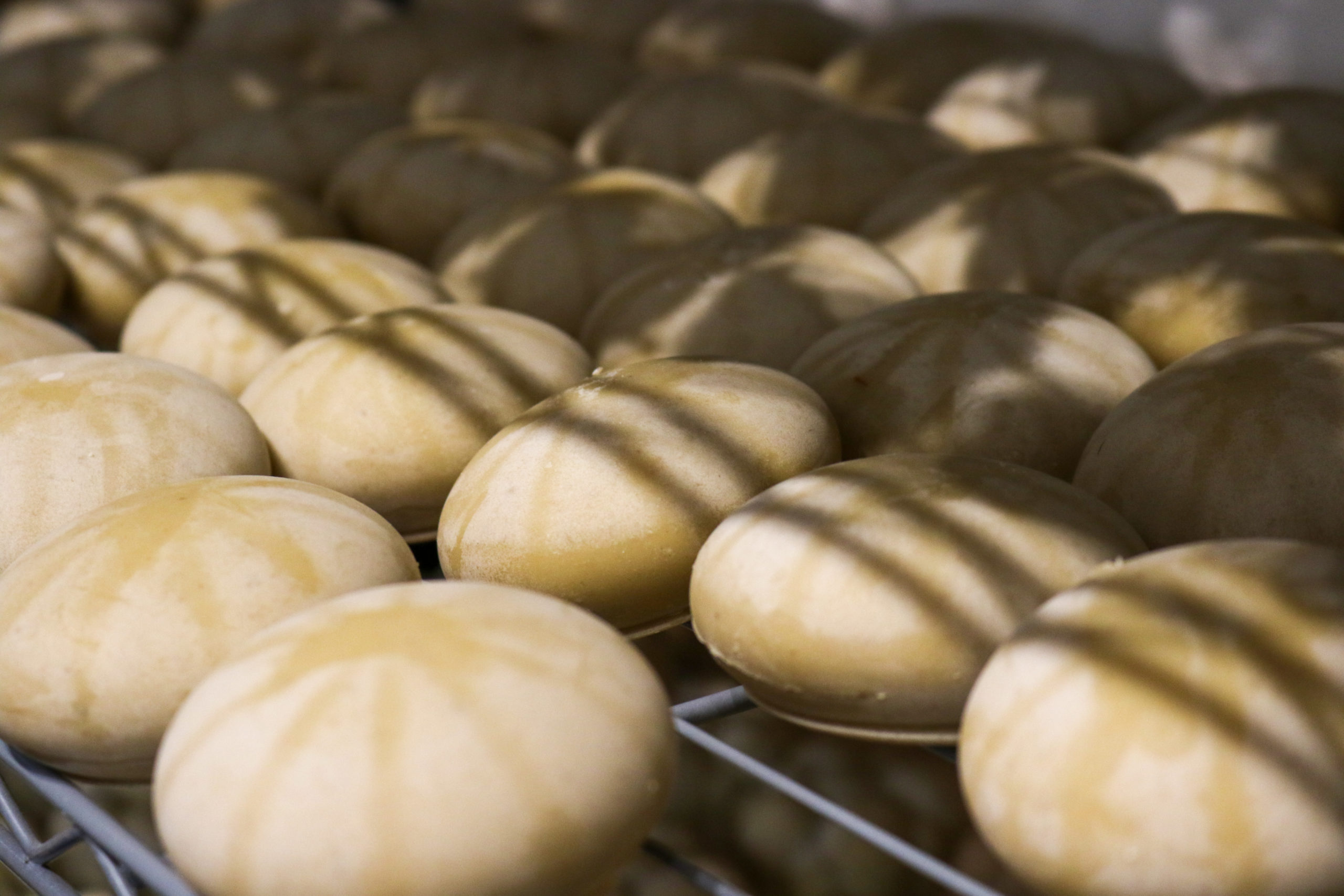
Avantages de la saponification à chaud
Contrairement à la saponification à froid qui nécessite une cure de 4 à 6 semaines (minimum), on peut utiliser le savon fabriqué à chaud presque immédiatement après sa fabrication. Les huiles essentielles ou fragrances (et autres additifs fragiles) peuvent être ajoutés à la fin du processus sans être dégradés par la soude. Cela préserve leurs propriétés et leurs parfums.
La saponification à chaud permet d’incorporer un excès d’huiles non saponifiées (appelé surgras) qui reste intact, offrant un savon plus hydratant. C’est cependant aussi le cas pour le saponification à froid : un ajout de corps gras en fin de processus, une réduction de soude dans les calculs, ou même les deux.
Inconvénients de la saponification à chaud
Le chauffage et la surveillance prolongée du mélange demandent un processus plus long et énergivore. Le savon à chaud peut avoir une texture plus rustique ou moins lisse que le savon à froid, ce qui peut ne pas plaire à tous les utilisateurs. La saponification à chaud est une méthode ancienne mais efficace que de nombreux artisans savonniers utilisent pour produire des savons naturels et faits main. Le savon de Marseille et d’Alep sont les exemples les plus connus.
Continuons avec la saponification à froid
La saponification à froid est aussi un procédé traditionnel de fabrication de savon qui consiste à mélanger à basse température (entre 30 et 40°C pour ma part) un ou plusieurs corps gras et une base. Ce processus permet de garder un maximum les propriétés des huiles qui composeront le savon. Par définition, un savon saponifié à froid est surgras (en moyenne, 8 à 10% de corps gras non saponifié). Soit on ajoute un corps gras en fin de processus, soit on réduit la quantité de soude dans les calculs de départ, soit on combine les deux.
Étapes du processus de saponification à chaud
Tout comme en saponification à chaud, il est nécessaire de préparer les huiles et les beurres qui détermineront les propriétés du savon, ainsi que la base alcaline, à savoir la soude caustique, généralement utilisée pour les savons solides. Chaque corps gras a ce qu’on nomme « un indice de saponification« , ce qui permet, de par leur poids dans la recette, de calculer le poids de la soude.
Mélange et trace
On mélange la soude à de l’eau froide (jamais l’inverse). Le mélange monte à très haute température très rapidement ; il faut rester vigilent et protégé pour éviter les éclaboussures (testé et désapprouvé). En parallèle, on mélange dans un récipient les cors gras. Lorsque le mélange de soude et d’huiles sont à températures égales, on mélange puis on mixe jusqu’à obtention de la trace. La réaction de saponification débute alors. Selon la dureté des matières premières (notamment le beurre de karité), la trace peut arriver très vite et cela rend compliqué le moulage.
Ajout des additifs
La trace apparait : on peut ajouter les additifs.
Pour les savons Snoap, les additifs sont des argiles (savon d’Antan à l’argile blanche, savon Rose, aux argiles rouge et blanche), des épices (savon Abelha, au curcuma), du charbon (savon Petit Automnal), des fleurs séchées (savon Dattier, à l’hibiscus). La fragrance fait aussi partie des additifs. Celle-ci peut aussi accélérer la trace, donc la pâte va durcir très vite et qu’il se peut que le savon soit très difficile à mouler.
Mise en moule et cure (obligatoire)
On coule la pâte dans des moules silicone, cependant d’autres savonniers utilisent la méthode de la découpe en barres.
24h à 48h plus tard, on démoule chaque savon que l’on pose sur une grille pour laisser la cure opérer : les savons sèchent minimum 5 semaines, voire plus selon la composition du savon. C’est la cure, qui contrairement à la saponification à chaud, est obligatoire pour laisser le processus se terminer et le pH se stabiliser. A la fin de cette période de séchage, on mesure le pH et celui-ci devra être située entre 9 et 10.
Avantages de la saponification à froid
La saponification à froid consiste à chauffer à basse température, ce qui permet de conserver intactes les propriétés des huiles végétales et des additifs naturels (huiles essentielles, argiles, extraits de plantes). Cela garantit que les bienfaits nourrissants, hydratants, et apaisants des ingrédients sont préservés dans le savon final. Lors de la saponification à froid, la glycérine se produit naturellement. Elle est un humectant, ce qui signifie qu’elle attire l’humidité de l’air vers la peau, aidant à la garder hydratée. Les méthodes industrielles retirent glycérine pour la vendre séparément. La saponification à froid conserve toute la glycérine dans le savon, ce qui en fait un produit très hydratant.
Inconvénients de la saponification à froid
Le temps de cure est long : minimum 4 à 5 semaines, voire plus. Difficile d’être spontané. De plus, la manipulation de la soude caustique peut s’avérer compliquée : en plus d’éclaboussures probables (qui brûlent la peau), les vapeurs engendrées par le mélange dans l’eau provoquées par la hausse de température en quelques secondes provoquent des difficultés à respirer. C’est pour cela qu’il faut se couvrir entièrement et porter un masque.
Il se peut que le rendu ne soit pas toujours efficace. Connaissez-vous mes savons Toumoches ? Ce sont mes ratés de fabrication. La saponification à froid propose parfois des résultats variables, malgré une même recette. Il faut rester attentif à sa façon de fabriquer : conditions globales, poids des ingrédients, température du mélange etc. Cela permet de garder un maximum un résultat cohérent. Et enfin, le coût de production reste tout de même plus élevé.
Et donc…
Tout est question de capacité de volume (fabrication et stockage) et peut-être de rentabilité de temps (= la cure). Les deux méthodes se valent très bien, tant que les matières premières sélectionnées sont qualitatives (et si possible provenant directement de producteurs), et que ce qu’on appelle « les bonnes pratiques de fabrication » sont respectées.